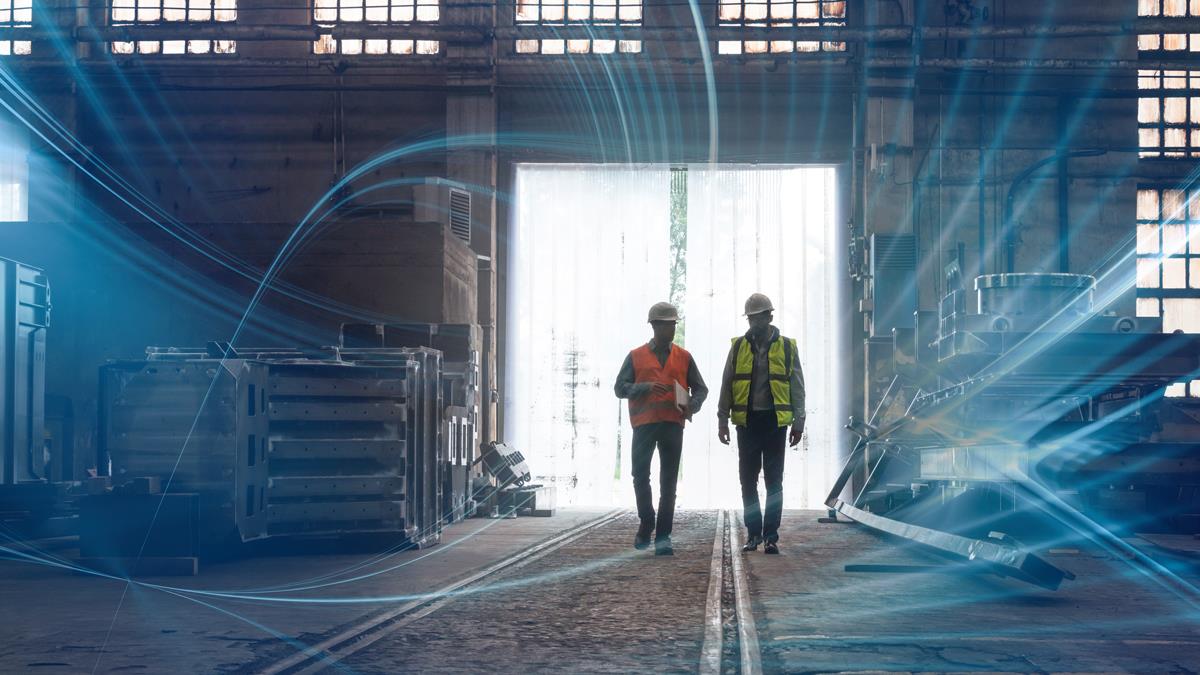
It’s been estimated that, globally, unplanned downtime costs companies millions in lost production hours and more than $800 billion in lost revenue. These major costs in productivity can mostly be attributed to incorrect and inadequate greasing of machinery. Before diving into solutions, it's important to know just what downtime is and the potential issues it can create.
Downtime in maintenance and reliability refers to the period of time when a machine, equipment, or an entire system is not operational or available for its intended use due to planned maintenance, unplanned breakdowns, repairs, or other reasons. Downtime is a critical concept in these fields because it represents a loss of productivity, efficiency, and often revenue for an organization.
There are two main types of downtime:
-
Planned Downtime: This downtime is scheduled in advance to perform routine maintenance, inspections, upgrades, or repairs on equipment. It is a proactive approach to ensure the continued reliability and performance of assets. During planned downtime, the goal is to minimize disruption to the overall operations and to complete the necessary maintenance as efficiently as possible.
-
Unplanned Downtime: This type of downtime occurs unexpectedly when equipment or systems fail, often due to unexpected breakdowns, malfunctions, or other issues. Unplanned downtime is costly and disruptive, as it can lead to lost production, increased maintenance costs, and potential damage to an organization's reputation.
Reducing or minimizing downtime is a key focus in maintenance and reliability management. Effective strategies and practices, such as predictive maintenance, preventive maintenance, condition monitoring, and reliability-centered maintenance, are implemented to maximize the availability and performance of assets while minimizing unplanned downtime. Minimizing downtime helps organizations maintain productivity, reduce costs, and improve overall operational efficiency.
I co-founded GreaseBoss to help eliminate unplanned downtime. The owners, managers, and operators across the various industries around the world I’ve talked to face this very challenge, 24/7. Although every business is confronted with different challenges, I believe the solutions are almost always the same: collaboration and innovation.
It was through collaboration and innovation that we enabled a tier-1 mining giant, eliminating the risk of the reoccurrence of a $30 million failure at one of their mines in Australia. They came to us after a minor, undetectable equipment failure in their automated lubrication system led to a catastrophic failure of one of the operation’s critical conveyors, halting mining production.
We responded to this request for help through collaboration and innovation. Here’s how we safeguarded this critical equipment and how we continue, through partnerships, to ensure these catastrophic failures don’t happen again.
Collaboration Is Critical
Our first task was to identify the core issue for these major failures and breakdowns in machinery. In this case it was established that it was just one lubrication point that was responsible for this catastrophic failure. A minor, undetectable component failure in one of the injectors blocked the grease line and starved the bearing of grease. The mine was facing an issue that we see time and time again across industries globally.
We were able to identify the failure and, in turn, provide a resolution to the issues through close collaboration with the mine. Through joint problem solving and technical works we integrated our Endpoint system to their lubrication points. Once initiated, we then went through three phases of field pilot prototypes to refine the product to final commercial readiness.
In short, Endpoint provided technology that gave the mine assurance that all was well with the lubrication of their machinery. Happy days. If something wasn’t right, the GreaseBoss system would flag it immediately and point to the specific source and location of the problem.
The collaboration continues. After successful launch and integration in the field, we are now working with the mine to integrate the data to display on their own operational SCADA system to form part of the day-to-day monitoring of the plant.
Endpoint on Apron Feeder. One major point of failure eradicated by a simple but powerful advance-warning system.
Innovation in Action
We took our innovative, cloud-based solution to analyze the exact volume of grease being delivered each pump cycle to every critical bearing on the conveyor. By automatically monitoring planned vs actual greasing on these critical bearings, we were able to develop insightful reports and alarming systems.

Designed to work in harsh environments, Endpoint uses world-leading flow meter design to measure and verify the flow of grease as it enters the machine. This data is automatically transmitted to the GreaseBoss Gateway, which has the versatility to work with many of the common connectivity protocols used in heavy industry.
All of the data was fed into and aligned with the mine's own systems through the API, which enabled both our respective teams to get data-driven insights on the mechanical breakdown issues, along with feedback on the types of grease being used and how it was performing.
Collaborate, Innovate, Replicate
After the 10-month pilot, we sat down with the mine’s managers and operators to review and reflect on our learnings. We collaborated on making adaptations to the original pilot and then, just as importantly, brought in additional innovations to improve and enhance the greasing processes. Through the innovation and collaboration at the original site, alongside the replication and extension to other parts of the mine, to date more thant $30 million in lost productivity and labor costs caused by the unplanned downtime have been eliminated.
This could not have been achieved if we had not been able to actively collaborate with the operators and managers on-site. It’s crucial for solutions providers like GreaseBoss to be viewed as a partner and not a supplier. I know that requires a level of trust that is not always easy to attain, however, by placing trust in our people, we were able to get the insights from the mines own systems and data. This, in turn, allowed innovation to thrive and develop.
Collaboration and innovation has made a material and financial impact at one site running to millions of dollars. However, I passionately believe collaboration and innovation will impact the smallest operation just as significantly as it would the biggest. It all starts with your mindset and attitude.
*source: The True Cost of Downtime (Senseye report, 2021)
About the Author