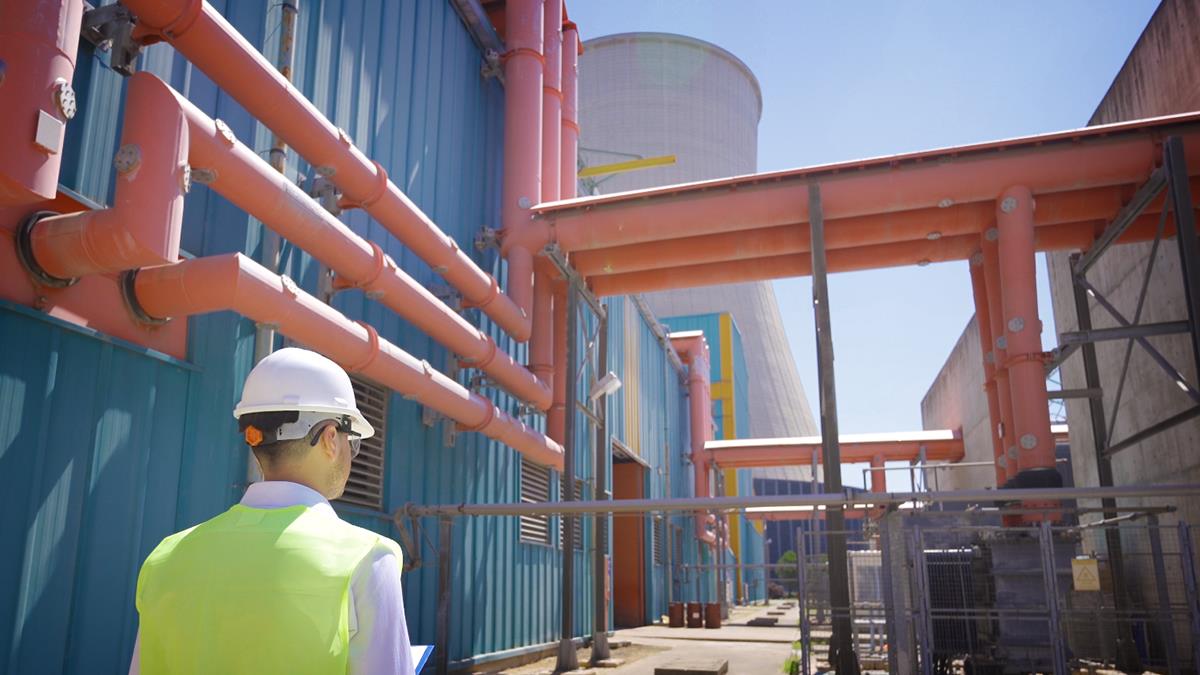
In the heart of every nuclear power plant lies a hidden challenge that plays a crucial role in the facility's safety, efficiency, and longevity: maintaining proper lubrication. While the nuclear power industry is renowned for its stringent safety measures and rigorous maintenance procedures, the complexities and unique challenges of lubrication are often underestimated. This article will delve into nuclear lubrication, exploring its critical role and the challenges engineers and technicians face in ensuring it functions flawlessly.
Radiation-Induced Breakdown
The most prominent challenge in nuclear lubrication is the pervasive presence of ionizing radiation. Nuclear power plants are environments where radiation is a part of daily life, and this radiation can have a detrimental effect on lubricants. Radiation-induced breakdown of lubricants can lead to their degradation and the loss of their lubricating properties. This poses a significant challenge for the industry, as maintaining consistent lubrication under such conditions requires specially designed radiation-resistant lubricants.
Contamination Control
Nuclear power plants adhere to
strict contamination control measures to prevent foreign materials from entering critical systems. Contaminated lubricants can be a serious issue, causing equipment damage and system failures. Therefore, ensuring that lubricants remain uncontaminated is a constant challenge. Lubrication engineers must employ sophisticated filtration and purification techniques to maintain the purity of lubricants in such a sensitive environment.
Extreme Temperatures
Nuclear processes often generate extreme temperatures, which can harm conventional lubricants. High temperatures can cause
lubricants to break down, lose viscosity, and ultimately fail to protect the equipment. Consequently, special high-temperature lubricants are required to ensure that components function optimally under these conditions.
Cryogenic Conditions
Conversely, some nuclear applications operate under cryogenic conditions, particularly in research reactors, where extremely low temperatures are the norm. Conventional lubricants can become brittle and lose their lubricating properties in such conditions. Lubricants specifically designed for low-temperature applications are essential to ensure that equipment continues to operate efficiently.
Chemical Compatibility
The nuclear industry employs various chemicals, including coolants and moderators, in its processes. Unfortunately, some lubricants can be incompatible with these chemicals. This challenge necessitates carefully selecting lubricants to ensure they are compatible with the specific environment in which they will be used.
Long Service Life
Nuclear equipment is designed to have an extended service life, often spanning several decades. To meet these long operational requirements, lubricants must provide long-lasting protection and lubrication without degrading over time. This presents the challenge of selecting and formulating lubricants that can endure for years without performance degradation.
Safety and Regulatory Compliance
The nuclear industry operates under stringent safety regulations and guidelines. Proper lubrication is critical to maintaining safety, and nuclear facilities must ensure that their lubrication practices comply with regulatory requirements. The challenge here is in adhering to the rules and demonstrating and documenting compliance with regulatory bodies.
Inaccessible Locations
Nuclear facilities often contain components in hard-to-reach or confined spaces, making lubrication and maintenance tasks exceedingly challenging. Access to these areas may be limited due to radiation risks, equipment design, or other factors. Engineers and technicians must develop specialized tools, equipment, and procedures to address these hard-to-reach locations.
Monitoring and Inspection
Continuous monitoring and inspection of lubrication systems are essential to identify issues early and prevent equipment failures. This can be challenging in nuclear facilities due to the high radiation levels that can limit human access to certain areas. Engineers often employ remote monitoring technologies, robotics, and other advanced techniques to ensure the integrity of lubrication systems.
Environmental Impact
Lubrication spills or leaks in a nuclear facility can have severe environmental and safety consequences. Addressing the environmental impact of lubrication practices is a challenge in itself. The nuclear industry must not only contain and remediate any lubricant spills but also develop strategies for minimizing the impact of lubricant use in the first place.
Supply Chain Concerns
Sourcing specialized lubricants and materials for nuclear facilities can be challenging due to their unique requirements. Nuclear lubricants must adhere to strict standards and regulations. Supply chain disruptions can have cascading effects on the maintenance and operation of nuclear facilities, which makes ensuring a robust supply chain a top priority.
Solutions and Innovations
The nuclear industry has risen to meet these challenges with a combination of innovation, technology, and rigorous procedures:
- Radiation-Resistant Lubricants: The development of lubricants specifically designed to resist radiation-induced breakdown has been crucial. These lubricants can withstand the high radiation levels in nuclear environments, ensuring longevity and reliability.
- Advanced Filtration and Purification: Nuclear facilities employ state-of-the-art filtration and purification systems to maintain the purity of lubricants. These systems help remove contaminants and particles that might compromise equipment performance.
- High-Temperature Lubricants: Specialized lubricants operating at high temperatures have been developed to protect critical components in nuclear reactors.
- Low-Temperature Lubricants: Lubricants designed for low-temperature environments are necessary for cryogenic applications. These lubricants maintain their fluidity and lubricating properties in extremely cold conditions.
- Chemically Resistant Lubricants: Lubricants are formulated to be compatible with the specific chemicals used in nuclear processes, preventing undesirable chemical reactions and ensuring equipment integrity.
- Long-Lasting Formulations: The nuclear industry collaborates with lubricant manufacturers to create formulations that can withstand long operational lifespans without degradation, reducing the frequency of maintenance and replacement.
- Robotic Maintenance: Inaccessible locations are addressed through robotic systems designed to perform lubrication and maintenance tasks in high-radiation areas without risking human health.
- Remote Monitoring: Advanced sensor technologies and remote monitoring systems enable engineers to monitor lubrication systems closely without direct access to high-radiation zones.
- Environmental Stewardship: The nuclear industry is increasingly focused on minimizing its environmental impact. This includes developing lubricants that are less harmful in the event of spills and taking measures to prevent such incidents.
- Diversified Supply Chains: Nuclear facilities often work to diversify their lubricant supply chains to mitigate the risk of disruptions. This can involve sourcing from multiple suppliers or maintaining strategic stockpiles.
Conclusion
Proper lubrication in the nuclear power industry is a hidden yet critical aspect of safe and efficient operation. The challenges of radiation, contamination control, extreme temperatures, and other factors are met with innovation and rigorous procedures. As the industry continues to evolve, the focus remains on finding solutions that ensure the integrity and safety of nuclear facilities, and lubrication plays an essential role in this endeavor. Understanding and addressing these challenges is essential for the nuclear power industry to continue providing clean and reliable energy while maintaining the highest safety and environmental responsibility standards.
About the Author