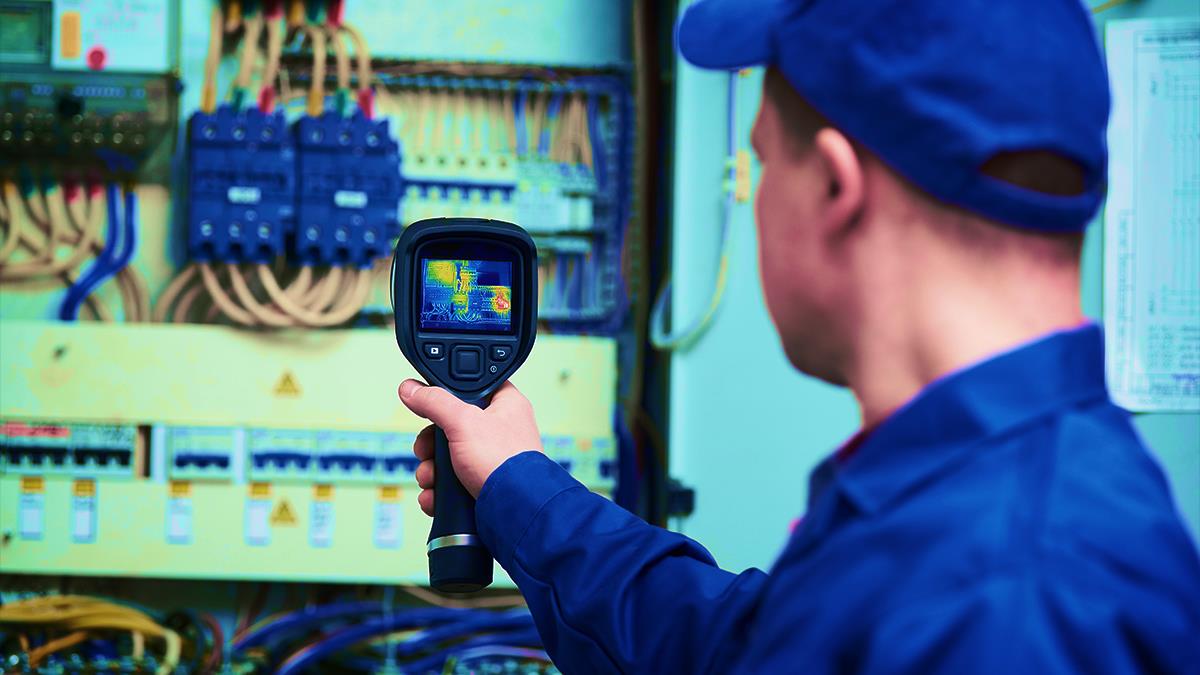
Electrical safety and energy conservation are significant concerns in industrial manufacturing. Common issues like partial discharge and compressed air leaks are known to threaten employee safety and machine health; however, traditional methods of identifying these hazards can be time-consuming and inefficient. Ultrasound technology offers a reliable and cost-effective solution for detecting potential hazards early, reducing the risk of equipment failure and worker injury.
What is Partial Discharge?
Partial discharge (PD) is a serious phenomenon that can damage critical machinery and threaten
employee safety. PD occurs when a small insulation area in a high-voltage environment can’t handle the electrical stress and begins breaking down. It’s referred to as “partial” because it doesn’t span the whole distance between two insulated electrodes.
This causes the insulation to deteriorate over time, resulting in total failure. If you don’t identify the problem promptly, insulation failure can result in loss of power supply and serious physical harm to employees.
Types of Partial Discharge
There are three distinct types of partial discharge:
-
Corona – This common form of PD occurs when discharge emits from the conductor’s surface directly into the air. The electric field at a conductor is greatest where the curvature is sharpest, meaning that corona discharge will first occur at sharp points, corners, and edges.
-
Tracking – Surface tracking can be one of the most destructive types of PD and occurs when discharge travels along the surface of the insulation. Contamination and insulator surface weathering are the two most common causes of tracking.
-
Arcing – Arcing discharge is a prolonged electrical discharge produced by the electrical breakdown of a gas. When this current flows through the air or any other normally non-conductive medium, it forms plasma.
Dangers of Partial Discharge
The effects of partial discharge can be highly detrimental; when PD occurs, it effectively changes the nature of the insulation medium. Left unchecked, the insulation cannot withstand the stress from the high voltage, and a complete failure occurs. This final breakdown is catastrophic, causing large-scale damage to equipment and a danger to personnel.
Damaging partial discharge can cause:
-
Unplanned downtime
-
Facility fires
-
Insulator degradation
-
Grid overload
The thing to remember is that these dangers are completely avoidable with the right inspection tools. Advancements in
ultrasound technology have allowed us to detect partial discharge before a threat is posed, protecting machine health, employee safety, facility productivity, and profitability.
Improving Workplace Safety with Ultrasound
A reliable solution for preventing the dangers of PD is ultrasound technology. With an acoustic imaging camera, you can protect the invaluable safety of your personnel and efficiently detect issues such as corona, tracking, and arcing
before severe damage occurs. These partial discharge emissions produce high-frequency sounds, which ultrasound equipment can detect and translate into audible ranges. These ranges can then be heard through headphones and recorded to determine the threat’s severity.
One of the largest misconceptions surrounding ultrasound technology is that it’s difficult to operate or requires extensive training. In reality, these solutions can be as simple as pointing a camera at an electrical asset and reading the screen, revealing the location of the partial discharge. The camera can even distinguish a PD from other ultrasound sources, reducing false positives and allowing you to maximize your
maintenance schedule and budget.
Energy Conservation Made Easy
Aside from ensuring electrical safety, an acoustic imaging camera can also help conserve energy by detecting air leaks, a significant problem that affects most industrial facilities. If your compressors are having a hard time keeping up with the demand being placed on them, air leaks are the most likely culprit. 1 kW of compressed air is eight times more expensive than 1 kW of electricity, and about
30% of all compressed air is lost to leaks. Rising energy prices can quickly make compressed air your facility’s most expensive utility.
Acoustic imaging cameras provide an easy way to find compressed air leaks (or any other compressed gas). Simply switch on the camera and watch the leak locations show up on the screen. These cameras will show you the decibel level, rate, and estimated leak cost for each compressed air leak.
Not only do compressed air leaks cost money, but they also:
-
Reduce equipment running hours.
-
Add unnecessary wear and tear to your equipment.
-
Potentially present a safety risk to employees.
Utilizing simple point-and-scan technology to locate and fix compressed air leaks will reduce the effects of rising energy costs, create a safer working environment for all employees, and ensure your facility is running at optimal efficiency.
About the Author