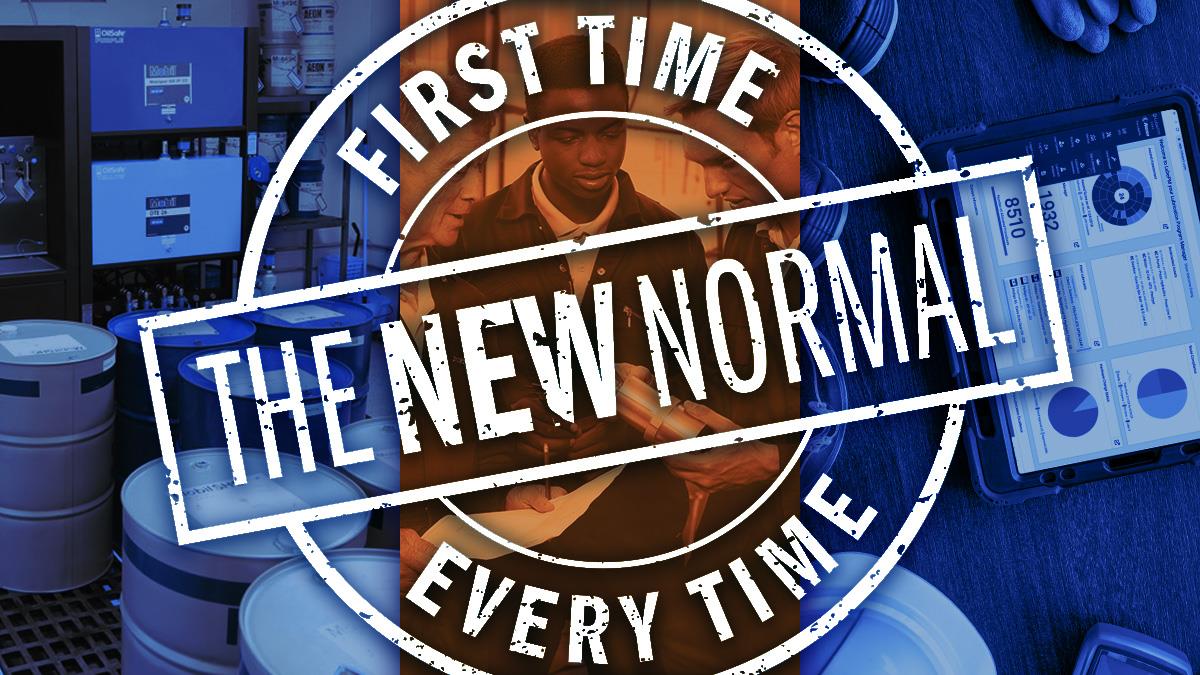
The term "the new normal" has been used countless times over the last several years. In the workplace, this has included analyzing many business principles and changing organizations to allow such things as working from home, having a social impact on your work, and focusing on mental health. These items are good, and some industries have more latitude to make changes than others. In our realm, the new normal is still very much the same business as usual. Components fail, production lines go down, and reactive maintenance is still the norm in too many facilities. This leads to an environment where workers can become desensitized to failure and begin to accept that little can be done to address them, let alone improve the daily grind by breaking this cycle.
This is further compounded by the lack of skilled professionals being able to backfill openings that, in some cases, have gone unfilled for years. Recently, I was in a facility that has been trying to hire multiple mechanics and operators just to get their staffing levels up to pre-2020 levels. It is the same song, different verse in many plants where headcount reductions or vacant openings have left the remaining employees doing more with less. Over the past several decades, there has been a "leaning" down of organizations where headcount has been replaced with efficiency and tools to make the workforce more effective. This is a good effort but still requires skilled professionals to operate and sustain the facility.
Economic Shifts and the Need for Efficiency
If anything, the need for improved processes and skilled people will only escalate. Goldman Sachs released a statement saying that the economy is returning to a pre-2008 environment (
US Economy, Markets to Return to Pre-2008 Conditions in 2024: Goldman Sachs). Recent legislation, such as the Inflation Reduction Act, has spurred a new level of investment into many businesses, including pharmaceuticals and those critical to infrastructure. All signs point to a future where it isn't necessarily sustaining the current production but increasing it significantly. With organizations still hesitant to increase headcount, the compass points even more to empowering our staff and looking towards options to help improve efficiency and reduce downtime in every place possible.
Analyzing the work is one of the first places to look for improvements.
The True Cost of Poor-Quality Work
When we perform
lubrication assessments, we often find areas where work is unnecessarily performed. For instance, it is common to find greasing activities performed far more frequently than needed. This is costly in terms of manpower and consumables — which are great savings areas and allow us to reallocate that manpower to other places where work isn't getting performed. The work analysis could begin with a review of all current PMs and simply look at the task frequency. From there, it gets more granular in ensuring the work being performed addresses known root causes of failure and is impactful enough to perform. This serves as the basis of a PM optimization process and is a way to uncover hidden manpower.
Adding staff can be a difficult task. Attracting talent has become a vast industry, with many companies employing recruiting agencies to help replenish headcount and fill jobs that have been vacant for a while. There are several ways to attract talent, but maintenance jobs are often viewed as "dead-end" or "dangerous" work. People want to know their work is valued, and what better role could someone have that makes a real difference in a company's profitability than in maintenance or reliability? Taking this a step further, utilizing newer tools such as tablets or laptops with the
latest maintenance software can attract younger professionals who may not realize how technological a job in this field can be. Utilizing tools and platforms that allow you to look into the inside of the machine to know what is wrong with it is a powerful motivator to get people to join your staff.
Proactive Maintenance Best Practices
Utilizing that same approach with onboarding can help break old habits as well. Instead of simply relying on a shadowing period, using technology to help people ramp up in capability can significantly increase productivity and minimize issues of poor-quality work. We designed our
lubrication management system to help onboard new lubrication technicians and enable them to perform the tasks correctly from the beginning. A cost associated with performing work incorrectly goes beyond wasting consumables or spending more time than is necessary.
Ultimately, the machines pay this price as improper lubrication continues to be one of the leading causes of equipment failure and unplanned downtime. In this case, we must do better than return to the status quo. Now is the time to improve our processes.
Breaking Old Habits: The Path to the "New Normal"
I believe the "new normal" should rigorously follow the proactive maintenance best practices. If we could just focus on five main things: keep the machine and lubricant clean, cool, and dry, and make sure the machine is aligned and balanced, our machines would run better, last longer, and we would start to find capacity where we originally were tapped out. Proactive maintenance requires diligence and all staff being on the same page because even just a single person doing something incorrectly can unravel all the work done by others. Education, awareness, and focus must be front and center with this approach.
This is nothing novel, but many don't know where to begin on this journey. Sticking with lubrication, a great place to start is
lubricant consolidation. This helps make sure we don't have unnecessary lubricants on hand. The most visible place to make changes is in the lube room. This is the heartbeat of any lubrication program, and this room should be the cleanest area in the plant. Everything should have a place, and effort must be given to keep it in order. With PM optimization, a detailed review of the equipment can help ensure we are doing the correct work and using the correct products. The enemy of these improvement efforts is complacency and competing priorities. Let's break the "this is the way we have always done it" and make the "new normal" doing the work the right way, the first time, every time.
About the Author