One of the most important pieces of information in oil analysis is the amount of operating time on the lubricant, which is typically reported in hours or miles/kilometers. The time that the lubricant has been in service, or "lubricant time", is vital to determining the severity of a wear or contamination condition and whether maintenance action is warranted.
Consider the following scenario: A mobile hydraulic system has 50 parts per million (ppm) of silicon/silica (dirt), which would be a cautionary level for a lube in service for 500 hours. However, if the lubricant time reported was only 25 hours, the 50 ppm of silicon is a more severe condition. A recommendation of investigating and correcting the source of contamination would be appropriate.
The lubricant in a diesel engine is changed and tested regularly every 10,000 miles and no abnormal conditions are identified. A decision is made to increase the drain and testing interval to 40,000 miles. The corresponding oil analysis report shows a remarkable increase in bearing metal (lead, tin, copper).
Knowing the lubricant miles quadrupled, a recommendation to monitor the oil pressure, reduce the drain interval and resample in 10,000 miles would be in order. If lube miles had not been reported, the analyst may have recommended that the bearings be inspected - a much more costly and time-consuming maintenance recommendation.
Calculating the rate of wear (ppm of metal per 1,000 miles on the oil) during an oil drain interval, or the rate-of-change of wear between oil samples taken during a single oil fill, can be a valuable interpretation tool.
After 250 hours of service, the oil is drained from a diesel engine and sent to a laboratory for testing. The spectrographic metals test reveals the engine has a severe coolant leak (sodium/potassium). A month later, another oil sample is taken and sent to the laboratory for analysis. The second test reveals a 50 percent reduction in coolant indicators (sodium/potassium). Depending on the number of hours on the lubricant, several conclusions can be drawn from the significant drop in coolant metals.
First, if the amount of time on the lubricant is equal to the number of hours on the prior sample (250 hours), then the coolant leak was most likely rectified. Some residual coolant metals would still be present if the system was not flushed thoroughly. Draining the oil and thoroughly flushing the system would be recommended to remove any residual coolant.
A second possibility also exists. If the amount of time on the lubricant is reported to be significantly less - for example, 75 hours - a much more severe condition exists. The reduction in coolant metals could then be attributed to less time on the lubricant and the assumption made that, most likely, the coolant leak was not corrected.
The recommendation would then be to perform further diagnostics to determine and correct the source of coolant contamination. Again, the key factor in determining the proper course of action depends upon knowing the amount of time on the lubricant.
Tracking and reporting lubricant time on industrial equipment was once difficult to monitor. This information has become more conveniently attainable with programmable logic controllers (PLC). A simple counter circuit can be programmed to monitor the amount of time a lube pump operates. It can then be reset every time a lubricant is changed.
However, lube time can still be monitored even if the equipment does not have a lube pump. The counter could be programmed to count the number of hours the main motor operates - the rational being that as long as the main motor is operating, lubricant is being used.
The preceding examples illustrate not only the importance of tracking and reporting lubricant time for oil analysis but also the difference omitting this information can make. In the first example, a cautionary contamination condition is determined to be more severe because of low lubricant time.
In the second example, a potentially costly equipment inspection is avoided because the significant increase in wear is qualified by increased lubricant time. Reducing the drain interval is determined to be the more appropriate maintenance action to take.
The third example illustrates the significance of lube time in detecting a contamination condition that might otherwise be allowed to continue. By providing lube time, premature failure is avoided with a proper maintenance recommendation.
About the CompanyJason Papacek is a data analysis manager for Polaris Laboratories. The company provides testing and analysis for oils, fuels, coolants and water-based fluids. For more information: www.polarislabs.com.
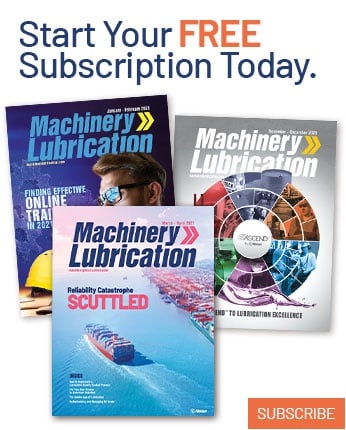