Each year millions of dollars are spent for new plant equipment designed to build things better and faster. However, machines continue to break down.
Bearing failure is a major cause of equipment downtime in today’s industrial environment, most often resulting from improper lubrication. Improper lubrication scenarios include the contamination of the lubricant by dust, dirt and moisture, inadequate amounts of lubricant applied to the bearing, and/or overlubrication of the bearing.
Each bearing failure directly impacts the production cycle. While bearings can be expensive, replacement cost alone is often miniscule compared to lost production and the cost to repair the damage.
Why, in the age of technology, is this a problem? It is because many bearings are still lubricated manually. No matter how diligently a maintenance staff adheres to a lubrication schedule, it is a difficult task. Because employees are expected to manage multiple responsibilities in the lean environment of today’s plants, it is common that proper lubrication is not considered a priority.
Benefits of Automated Lubrication
Every bearing, regardless of size or location, needs to be lubricated properly. Improper lubrication will result in high, yet unnecessary costs for the operation. Some of the direct costs resulting from improper lubrication include replacement bearings, labor for replacements and repair, excess lubricant and labor for inefficient manual practice. Some of the indirect, but very real costs are downtime or lost production; product spoilage due to excess lubricant; environmental, safety or housekeeping issues; and excess energy consumption.
While grease guns and manual lubrication seem to get the job done for many maintenance operations, their benefits often cannot compare to those provided by an automated lubrication system in terms of productivity, environmental issues and worker safety. An automated lubrication system helps to prevent bearing failure by providing the right amount of the right (fresh, clean) lubricant at the right time to the right place.
The main difference between automated and manual lubrication is that in the case of manually applied lubricants, technicians tend to lubricate on schedule (once a day, week, month, year, etc.) rather than when the bearing needs it. To compensate, the operator often will fill the bearing until he sees lubricant seeping out. The lubricant could be effectively “spent” by the time the operator gets back to it again. This sets up an overlubrication and underlubrication scenario. Conversely, automated lubrication provides lubricant constantly at an appropriate amount that allows the bearing to operate at its optimum. When the bearing is properly lubricated in this manner, it also helps to seal the bearing from contaminants.
Maintaining proper lubrication on production equipment reduces the number of breakdowns due to bearing failure. In addition, there is less downtime due to the manual lubrication process, as well as substantially reduced man-hours required for the task.
Automated lubrication is more precise and eliminates the cycle of overlubrication and underlubrication that contributes to bearing failure (Figure 1).
|
It also prevents excess lubricant from finding its way onto the finished product, the plant floor or other work surfaces. This results in fewer rejections, cleanup and disposal problems, as well as less waste of lubricant. And of course, all of this positively affects the company’s bottom line.
Another benefit of an automated lubrication system is worker safety. It becomes unnecessary for employees to engage in the potentially hazardous practice (Figure 2) of manually applying lubricant while machinery is operating or in hazardous, difficult-to-reach locations.
Example of Estimated Savings
When considering the benefits of implementing an automated lubrication system, it is important to know that it could pay for itself within the first year through the cost savings it generates. Production uptime, preventive maintenance costs, repair costs, safety expenses, environmental compliance costs, lubricant costs and machine replacement costs are all positively impacted.
For example, it’s not unusual for process plants like paper, petrochemical or primary metals to replace 1,000 bearings or more per year on the average. Depending on the application and size, each replacement bearing costs anywhere from a few dollars to several thousand dollars. An average replacement costs approximately $150 (material cost). It takes approximately three hours for a worker to replace each bearing. We can calculate the average cost to replace each bearing in the following example:
$150 per bearing + 3 hours average replacement time at $30 per hour labor cost ($90) = $240 per bearing
Total Annual Replacement Cost for 1,000 Bearings = $240,000
Reducing the number of bearings to be replaced by just 50 percent nets a savings of $120,000/year just on labor and bearing costs.
Downtime in the process industries costs from $10,000 to $150,000 or more per hour. Assuming a line production time value of $60,000 per hour, shutting down a strategic line for just three hours to replace a few bearings can be very costly. Consider that $60,000 x 3 hours = $180,000 in lost production.
There is no standard for the cost of a lubrication system. Very small systems can cost as little as $1,000, whereas large systems may cost tens of thousands of dollars. It becomes a fairly simple matter to justify the cost of an automated lubrication system. Obviously, the most important factor is how many bearings or other lubrication points need protection. Then, depending on the scale of the application, other accessories/controls may be required to maintain, monitor and manage the lubrication system.
Automated lubrication systems can lubricate a lone strategic bearing, all the lube points on an individual machine, or they can be designed to cover a process line or an entire plant, literally lubricating 1,000 or more points from a single system. Automated systems can be driven by a simple pump with an integrated timer or can involve a pumping system placed on a large bulk lubricant storage tank that might feed thousands of lubrication points. The centralized lubricant pumping system is more likely to be operated by a dedicated microprocessor controller or a machine/process PLC or a combination of both.
Other factors affect the cost of the lubrication system. The user could choose to monitor the system by visual verification of delivery or use automated equipment to indicate when a lubrication cycle does not occur as planned. It is definitely an issue of scale. The more lubrication points fed by a single system, the more likely the application can justify the cost of a more sophisticated control and monitoring system. The nature of the bearings themselves, their cost, the value of any given machine or series of machines and the total output value for a given production line are determining factors. Often systems are evaluated on a cost per bearing or lubrication point basis.
Automated Lubrication System Options
![]() Figure 3. Single-line Parallel System Pump unit with controller and small injectors likely used to lubricate an individual machine. |
|
Once the decision to automate lubrication processes is made, there are several options from which to choose. Available systems include: single-line parallel, two-line parallel, single-line progressive, mist lubrication, minute-volume/low-pressure spray, recirculating oil, pump-to-point (box) lubricators, single-line resistance and single-point lubricators. A brief description of each follows.
Single-line parallel.
This system is easy to design, install, maintain, modify or expand. It typically operates at high fluid pressures and can be used with grease or oil. In this system (Figure 3), the pump pressurizes the main supply line, and a piston inside the primed injector (Figure 4) displaces a premeasured amount of lubricant through the outlet to the bearing. The pump turns off and the supply line pressure is vented back to the reservoir. The spring-loaded piston returns to rest and the discharge chamber fills with a measured charge of lubricant for the next cycle.
Advantages:
- Easy to design
- Easy, cost-effective installation
- Individually adjustable injectors
- Proven, dependable design
Disadvantages:
- May not be suitable for combinations of heavy lubricants, very cold temperatures, very long supply line runs between pump and injectors
Two-line parallel.
This system is ideal for long pumping distances and extreme temperatures (Figure 5). It is easy to adjust to meet specific bearing requirements. It provides high pressure, up to 5,000 psi, and is designed to work with many lubrication points over a wide area. This system’s pump pressurizes metering devices through one side of a four-way, two-position reversing valve (Figure 6) and the first supply line. The metering device control piston shifts and directs pressurized lubricant to the main piston, which displaces lubricant to the bearing. Lubricant on the other side of the control piston is vented back to the reservoir through the second supply line and the other side of the reversing valve. The reversing valve shifts and the pump pressurizes the second supply line, repeating the cycle in reverse.
Figure 6. Two-line Reversing Valve. Directs the flow of lubricant from one side of a two-line system to the other.Advantages:
- Easily handles very viscous (heavy) greases
- Can accommodate long supply line runs between pump and metering devices
Disadvantages:
- May not be most cost effective for smaller systems
- Requires two supply lines (another cost)
Single-line progressive.
This economical and flexible option is a system that can be used with low-pressure oil, grease or high-pressure oil (Figure 7). The latest designs include a preassembled pump, controller and mono-block piston-metering device. The pump of this type of system provides a measured single shot, pulsed or a continuous volume during the lubrication cycle. The first primed piston in the block shifts, displacing lubricant to the bearing and diverting flow to the next piston. The second piston shifts and diverts flow to the third. The sequence continues through the metering device (Figure 8) until the timer or feedback switch stops the pump.
Figure 8. Progressive Divider Valve Installation. Installation can be completed using special, flexible lubrication line or high-pressure hydraulic pipe.Advantages:
- Accommodates a wide range of system control/monitoring options
- Can identify blockage by monitoring a single point
Disadvantages:
- One blockage can disable the entire system
- Large systems may require complex piping/tubing runs
Mist lubrication.
Another simple system, mist lubrication facilitates low oil consumption and cool running bearings. Mist is generated with heat and/or air currents and is carried through pipe to the lubrication point with low-pressure air. Then it is sized to the appropriate droplet before it is dispensed to the bearing. Closed loop systems are environmentally friendly because they return the mist to the generator.
Advantages:
- Cools and lubricates bearings
- Low pressure keeps pipe material cost down
- Positive pressure helps keep contaminants out of bearings
Disadvantages:
- Environmental/health concerns of “stray mist,” especially with nonclosed loop systems
- Oil only
- Sensitivity to flow, viscosity, pressure variables
- Extra pipe cost for closed loop systems
Minute-volume/low-pressure spray.
This system applies the precise amount of oil required by the lube point and has very low oil consumption, as much as 90 percent less than other methods. Environmentally friendly, this system is ideal for chain lubrication as it penetrates the wear points without overlubrication. When the timer signals the start of the lubrication event, the injector begins cycling, feeding oil at a controlled rate through small diameter tubing to the spray nozzle. Simultaneously, regulated low-pressure air is directed to the nozzle that mixes oil and air to produce a fine, controlled, nonmisting spray.
Advantages:
- Precise lubricant volume and application control
- No “stray mist” problems
- Fast, economical installation
- Very low lubricant consumption
Disadvantages:
- Oil only
Recirculating oil.
This system is used to lubricate rolling element bearings and to maintain correct bearing temperature. It features a motor-driven pump that provides a continuous supply of oil through a filtration and piping system to flow meters. The flow meters control the amount of oil entering the bearing. The oil exits the bearing and returns to the reservoir through another piping system and return filter. Heat exchangers and/or heaters are used to maintain correct oil temperature. These systems are common on large, heavily loaded bearings in process industries.
Advantages:
- Provides both lubrication and temperature control
- Conditions, extends life of oil
Disadvantages:
- Most are major, capital installations
- Some technologies require frequent manual adjustment at each flow meter
|
Pump-to-point lubricator.
Handles multiple lubrication points independently and is ideal for remote locations (Figure 9). This system, which can overcome high back pressures, features an individual, adjustable lubricator pump for each point. Pump-to-point lubricators use an electric motor or machine power take-off to rotate a cam running through the drive box/reservoir. The cam actuates individual pump plungers through a rocker mechanism. A plunger then draws oil through a needle valve and sight glass and dispenses the measured volume though a high-pressure tube to the lubrication point. It is commonly used on large compressors and stationary gas engines.
Advantages:
- Overcome extremely high backpressures
- Simple, rugged design
Disadvantages:
- Limited number of lubrication points
- Relatively high cost per point
Single-line resistance.
A simple and cost-efficient system. Designed for closely clustered bearings, this system offers a variety of flow resistance metering devices and can utilize manual, electric or pneumatic pumps. The pump supplies a fixed volume of oil to the metering device through low-pressure tubing. The level of resistance in the metering device determines the proportion of oil flow to each lubrication point.
Advantages:
- Simplicity
- Low price
Disadvantages:
- Oil only
- Reliance on resistance rather than piston metering devices can lead to nonpositive distribution of oil
- System size limitations
Single-point lubricator.
This is a simple and cost-efficient solution for individual, remote bearings. A completely self-contained unit, the single point lubricator is installed at each lubrication point. Gas pressure, spring or electromechanical power delivers the lubricant over time to the bearing. The reservoir or the entire unit is replaced when the lubricant is consumed, depending on the lubricator style.
Advantages:
- Low purchase price
- Easy to install
Disadvantages:
- Temperature will affect the volume output/service life of many single point lubricators
- Replacement cost rapidly exceeds cost of fully automatic, central systems if the number of lube points increase
Maintaining Automated Lubrication Systems
Maintenance of automated lubrication systems varies greatly from one system to the next. However, there are some common factors that can impact system performance and reliability.
First, the lubricant selected must be compatible with the intended application, the lubrication system components, system layout and ambient operating temperature range. When selecting a lubricant for a machine already equipped with automated or centralized lubrication, make sure the lubricant grade is approved for use with the specific lubrication system.
When changing lubricant brands or types, be certain that the new lubricant is chemically compatible with the old. Although you may be adding the new lubricant to an empty and clean reservoir, residual old lubricant will be in the piping and metering devices.
All systems require clean lubricant. Be sure to follow correct handling and storage procedures because a lubricant that is contaminated by dirt or moisture can damage lubrication system components, or worse, machine bearings.
A routine check of all fittings and piping is recommended. Leaks adversely affect lubrication system performance, as well as cause housekeeping, safety and/or environmental problems.
Keep system reservoirs filled with lubricant by topping them off on a routine basis. If the reservoir runs dry, most systems will pump air into the piping and metering devices. Air pockets are compressible and prevent systems from developing required pressure and volume of lubricant delivery, and the system will not function properly until the air is purged.
Other maintenance issues vary, depending on the type of system in use. If the system is very basic, it may not have low-level indication or any other type of monitoring. These systems typically have transparent reservoirs or “sight glasses” and should be visually checked for lubricant level periodically.
On a single-line parallel system, the injectors have an indicator pin that comes out after each lubrication event so one can see that all injectors are cycling. A progressive system also may have indicator pins, allowing one to observe movement to verify system operation.
The larger single-line parallel systems use pressure switches or transducers in the supply line to indicate completion of a lubrication event. After reaching the prescribed pressure within an allocated period of time, a special controller resets and times out until the next lubrication cycle. If the system fails to reach the prescribed pressure, the controller activates an alarm. A limit switch attached to a cycle indicator pin can perform the same function on progressive systems.
Pressure-activated performance indicators also are a monitoring option on progressive systems. These devices, which mount parallel to the outlet port on the distribution block, are activated by high pressure, an indication of a blockage. When activated, the performance indicator either vents lubricant or extends a pin.
Many systems may include a reservoir low-level indication. With this feature, the system controller or independent indicator will signal the need to fill the reservoir. Many systems allow an audible alarm or signal light to make the alert more noticeable. Often, this same capability allows the user to route the alarm signal to the machine’s PLC or to a central control panel in the plant.
In systems with sophisticated controls, remote sensors can be added to verify that each system cycle results in lubricant reaching the intended bearing. If the sensor does not detect lubricant flow, a fault signal is generated. This capability requires dedicated hardware and software to interpret the sensor signals.
Summary
In general, automated lubrication systems offer superior features to manual lubrication. The benefits of automated lubrication include less downtime due to bearing failure, reduced man-hours required for the lubrication task, and increased worker safety, as well as reduced lubricant and cleanup costs. All of these positively affect productivity.
There are many variables to consider regarding equipment lubrication. Automation of the lubrication process can start out small and simple, and can be adapted over time to specific needs. Suppliers can help determine what will work best for each situation and can assist in cost-benefit analysis.
Maintenance of an automated lubrication system varies with each system. However, there are simple rules that apply to all systems such as compatible and clean lubricant, routine checks of fittings and piping and visual review of reservoirs.
The principle to remember is that smaller amounts of lubricant supplied more frequently results in better lubrication and lower overall maintenance costs.
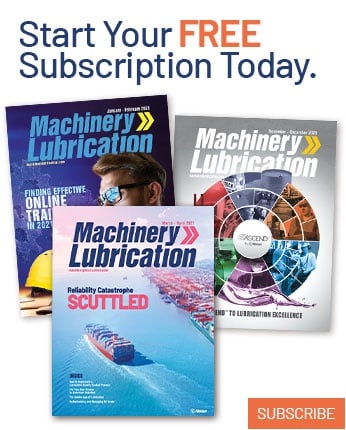