Simple modifications to breathers and sight glasses can be beneficial, but shaft seals are just as important in this process. Labyrinth-type seals are common devices for contaminant exclusion, and when properly maintained, they can greatly influence the reliability of the components in which they are installed.
A comparison of various seal materials (Ref. Seal & Survive, Seal School Handbook)
A seal’s function is multifaceted. Not only is it attached to a machine to keep particles and outside contaminants from getting in, but it also must keep what is inside the machine - whether it is oil, process fluid or a barrier fluid - inside.
One study by Exxon Mobil showed that the amount of oil lost is four times the capacity of the machine. The need for minimizing leakage while prolonging the machine’s operating life is more critical today, as the demands for reliability and the penalties for failure continue to rise.
Standard lip seals will limit certain contaminants from entering and restrict some leakage, but they are subject to failure, especially in systems with high pressure or extreme ambient conditions. One limiting factor of these types of seals is the construction material, with each elastomer having its own strengths and weaknesses.

What Is A Labyrinth Seal?
The basic concept of labyrinth seals is to reduce contaminant ingression not only by restricting the clearance through which particles enter but also by creating areas of turbulent flow to exclude contaminants. These types of systems provide better particle exclusion and less lubricant leakage than standard lip seals, which contact the shaft and rub the surface during operation.
Lip Seals vs. Labyrinth Seals
Shaft seals must be properly selected and maintained. Some seals do a good job of retaining oil or grease but do a lousy job of excluding contamination. Lip seals are a prime example, particularly the ones that are only directed inward. These types of seals tend to wear after a period of time because they make rubbing contact with the shaft. Eventually, the seals no longer function well from the standpoint of both oil retention and contaminant exclusion.
Lip Seal Labyrinth Seal
On the other hand, a labyrinth seal is non-contacting, so it will not have the wear-out condition. These seals are excellent for excluding particle contamination and moisture, even if there’s a spray of water nearby. So both oil retention and contaminant exclusion are at a much higher level of performance compared to contacting mechanical seals and lip seals.
Of course, the disadvantage of using labyrinth seals is that they are more expensive. Generally, you will need to retrofit these on the equipment and will incur the cost of their installation. However, labyrinth seals will last longer and perform better.
Labyrinth seals are constructed in multiple pieces. One piece, known as the stator, is affixed to the machine and remains stationary. The other piece, called the rotor, is attached to the shaft and rotates with the motion of the system. The two pieces interlock to effectively seal out the majority of contaminants while holding in the lubricant or process fluid.
These types of seals are non-contacting, which means that the two opposing faces do not touch each other. They are also considered frictionless, as the rotor and stator are separated by a very small gap. In many instances, this gap can be as small as 0.003 inches, which equates to roughly 76 microns. This may sound like a large opening in comparison to the 1-micron lubricant film inside a rolling-element bearing, but because of the path that the contaminant must take to actually reach the bearing, this gap is more than adequate.
All contaminants trying to enter the bearing housing must go through the seal’s maze (labyrinth) of turns and angles in order to reach the bearing. On the path through all of these turns, particles are constantly subjected to centrifugal forces due to the rotational motion of the shaft, and only a very small number make it through the entire length of the seal.
Types of Labyrinth Seals
A variety of different labyrinth seals are available, from bronze and stainless steel to plastic. The construction of the seals may even change between brands, with some employing magnets and others simply using O-rings to provide the necessary seat for the housing and shaft. However, they all operate on the same principle and must be properly installed to work correctly.
When looking for options to boost reliability and minimize bearing failures, consider the seals that are in use. In areas of high airborne particulate matter or heavy washdown areas, a labyrinth-style seal can help limit the ingress of contaminants and prolong machine life. With proper lubrication and contaminant-exclusion devices, many bearings can come close to achieving their design life.
How to Protect Stored Gearboxes with Labyrinth Seals
-
Spray shaft extensions with a suitable dry film or similar preservative.
-
For gearboxes with non-contact labyrinth seals, use internal vapor-phase rust protective coating instead of complete oil fill. Both oil wet and non-oil wet surfaces are protected by vapor-phase rust inhibitors.
-
Commercial vapor phase rust inhibitors include products such as Ashland Oil, Tectyl 859A or Cortec VP corrosion inhibitor. Typically, add 5 percent of the oil volume. Some inhibitors require the oil/inhibitor mixture to be heated and agitated in order to perform effectively.
This method may only be good for about six months and should be renewed if the storage period is longer. Another disadvantage is that it may cause incompatibility and foaming problems when filled with the service oil. Flushing is recommended before putting the gearbox into service.
References
EG&G Sealol, “Seal & Survive,” Seal School Handbook, Revision 3.
Fitch, J.C., Scott, R., & Leugner, L. (2012), “The Practical Handbook of Machinery Lubrication - Fourth Edition.”
Inpro/Seal, “Bearing Isolators.”
Maintenance Technology (1991), “Beyond Predictive Maintenance.”
Neale, M.J., “Drives & Seals: A Tribology Handbook.”
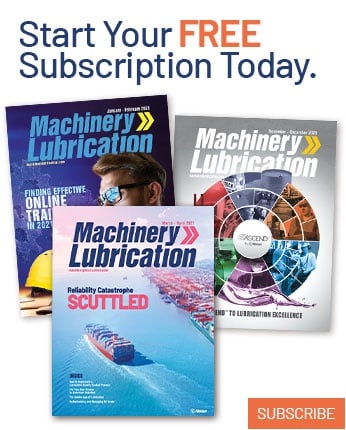