With so much emphasis put on selecting the proper lubricant, using lubricants approved by OEMs, and ensuring our lubricants arrive on time and with the correct properties, it is shocking that most organizations have no means to measure how well they are performing in these critical areas. Most lubrication professionals understand the importance of metrics as well as the importance of getting the right lubricant from the start, but most fall woefully short in ensuring these activities are scrutinized with any level of detail. As programs evolve and advance, they begin to track and score application, cleanliness, failure rate-the list goes on. However, these are all lagging metrics for your lubricant selection process. How can we flip this situation around and start looking at leading indicators for machine and lubricant health by focusing on lubricant selection?
Does your selection process pass the test?
Throughout my academic years, I was constantly measured. High test scores, timely submission of assignments and active participation are just a few examples of the unique blend of metrics and criteria I was expected to work toward. At the end of the semester, the final grade in the class was a reflection of my performance, not the performance of the instructor. When entering college, I learned of a web service that allows students to “grade” their professors. Finally, the shoe is on the other foot and I can get that feeling of karmic justice to bring to light those educators who upheld their end of the agreement to impart knowledge to the class. These services are very much alive today and are used by most students to determine which professor’s class to enroll in. This is analogous to our lubricant selection process. Our machines and technicians are “graded” against a curriculum based upon time between failure, cleanliness, safety-again, the list continues indefinitely. However, the lubricants used, the supplier of these lubricants and even the tools used to aid in selection are seldom scrutinized. We have the same scenario as the student to the teacher. The machines and technicians are the students, and the lube selection team and lubricant suppliers are the teachers. We need to look at both ends of the chain here and put metrics in place to ensure all parties are doing their tasks to the utmost of their abilities to pinpoint areas for improvement. Let’s boil this down to the two parties that should be reviewed and graded: the lubricant supplier and the lubricant selection committee. Understandably, most facilities may not have a lubricant selection committee, and the lubricant supplier may have been selected based upon ease or proximity to the plant. It’s unfortunate that such critical roles are simply left up to happenstance or reverted to “the way we have always done it.”
Lubricant Suppliers
In a previous article, I outlined the business case for why you should select a lubricant supplier that will partner with you on your reliability journey. This is a relationship that is of the utmost importance, especially as it pertains to getting the proper lubricant at the proper time with the proper support. In some cases, a supplier contract may be instated to target all these areas so there is an agreement of responsibilities between both parties. Think about your personal life and the amount of research you likely do prior to subscribing to a service or buying an expensive item. We typically gravitate toward the customer reviews. We read who had great service, who had a poor experience and what to be wary of when purchasing. If we were to review our lubricant supplier, what would a five-star rating even look like? What should they be judged against? Three critical items should be considered when deciding how many stars should be doled out.
On-time Deliveries
Perhaps the easiest metric to put in place is compliance of on-time deliveries. All lubricants are going to have a lead time associated with them, some of which may be up to a couple months depending on the type and where it is coming from. The impact this can have on our equipment is devastating. If we find ourselves in a situation where a lubricant is needed for start-up and the lead time is long, it often results in a suboptimum lubricant being used instead, and ultimately the machine suffers and the lubricant supplier takes the blame. Clear communication between delivery times and on-hand inventory needs to be had. Review the stated lead times in your agreement and cross that with the elapsed time between orders and deliveries. On-time compliance is a great leading indicator of lubricant inventory control and having the correct lube on hand.
Support
Most lubricant suppliers offer technical support with their products. Sometimes this support includes items such as oil analysis support (sampling and testing), training, field visits etc. If this support is relied upon to make maintenance decisions or just general knowledge transfer, the responsiveness and compliance of this agreement should be tracked and measured over time. For instance, if the supplier is to provide oil analysis sampling and test results for critical assets each month, we should be tracking the compliance of this occurring. The same holds true if there are to be scheduled learning sessions as well as general responsiveness for technical support by phone, email, site visits or any other means related to the agreement.
Contamination
It’s no secret that new oil doesn’t necessarily mean it is clean or defect-free. We should have a process in place to test incoming lubricants to make sure they meet the standards set for lubricants prior to putting them in service. While the supplier may not always have direct control over packaged lubricants’ cleanliness if they are not the point-of-fill, they do have some control to make sure deliveries are defect-free. One way this can be done is ensuring the fill-date is as recent as possible during reception. All lubricants have a shelf-life, and we want to make sure our supplier is giving us fresh lubricant in order to preserve the remaining shelf-life when it hits the plant. Reviewing the age of incoming lubricants, those that arrive dirty or wet, as well as those that arrive cross-contaminated with other fluids is a great metric to determine the quality control practices of the supplier. If the supplier scores well in all three of these areas, they earn the five-star rating. Remember these metrics should be reviewed, and any discrepancy should be shared with the supplier to put a plan in place for remediation. Even so, this rating only addresses half of the equation-now we need to think how our internal lubricant selection committee should earn their five-stars as well.
Lube Selection Committee
Oftentimes, the responsibility of selecting a lubricant is done by someone who isn’t as involved in the lubrication program as they should be. I’ve experienced lubricant selection ran solely by purchasing, whose main intent was simply to purchase the cheapest product they can, regardless of its performance. This line of thinking needs to end. If we are going to require our supplier to uphold their end of the bargain, we need to take our side seriously as well to ensure we are asking for the right products in the first place. Let’s start with deciding who should be on the committee to begin with. The committee should be comprised of the stakeholders in the lubrication program as well as purchasing. Typically, you would want to have representatives from reliability, maintenance, management, and purchasing to make all the decisions needed in a quick manner. It is understandable that there can be overlap between roles and variance in the structure of facilities, so finding the right blend of personnel for your committee may fluctuate a little. The end goal is to let everyone have a voice in the process who should and to keep in check any “drift” away from a specification over time. The big three things that should be tracked for the performance of this committee are below.
Selection review
There are many criteria by which a lubricant should be selected. Some major ones include: OEM Approvals Price Availability Brand Preference Performance Historical Use Consolidation Sometimes the simple act of selecting a lubricant for use can become an exercise in engineering chemistry crossed with materials science. Other times, people revert to whatever the OEM recommends and have over sixty different lubricants on-hand. The sweet spot is somewhere in-between. Ultimately, the committee needs to ensure the performance characteristics of the lubricant meet or exceed the demands of the equipment and are being purchased at the most reasonable rate. The above mentioned “drift” occurs when there isn’t a periodic, formal review of the lubricants in use or there isn’t anyone responsible for selection. This leads to complacency, resulting in frustrated technicians and failing machines. Measuring the lubricants on-hand against the needs of the machines should be performed annually at a minimum.
Training
It will be nearly impossible for the committee to do their job properly if there isn’t a plan on how they should increase their knowledge in the field of lubrication. Base oils, additives and greases are all evolving at a rapid pace, with new technology in their chemistry and performance changing the rules of how they traditionally have been used and selected. Without focusing on keeping our knowledge abreast of the changes, we will slip further away from the use of an optimum lubricant to something that might not give us the best performance for our dollar. A great way to track this is to measure the number of staff certified or, at minimum, trained in lubrication-specific curriculum. This should be reviewed to keep the knowledge current and applicable for all involved in the lubrication program.
Labeling
While we typically think about lubricant selection relating mostly to purchases, it’s important to remember that the technicians must select the proper lubricant from the lube room to apply to the equipment as well. Therefore, it is critical that the committee develop and implement a robust lubricant labeling program. Every lube point should be labeled, and the corresponding label should be found on the appropriate tools or product in the lube storage area. This helps ensure the correct lubricant is applied to the equipment, reducing accidental cross contamination in the field. The implementation of the labeling program should be measured and reviewed to make sure there is progress in this area. A periodic walk-down of the plant should be done to audit the labeling on the equipment and ensure any areas of deficiency are addressed. Provided that our committee performs well in these three areas, the five-star review is virtually guaranteed. Measurement and metrics go a long way to showcase areas of improvement and help us understand where we need to focus our efforts. Once we have a great supplier and a great selection committee, our technicians and equipment will reap the benefits resulting in less downtime, more engagement and improved culture throughout.
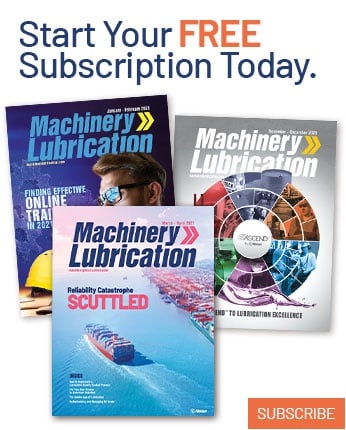