Throughout my many years of involvement with maintenance, repair, and operations (MRO) storeroom programs, one major fact stands out from the rest –MRO storeroom associates receive significantly less training than associates in other departments across the organization.
Often, MRO storerooms are seen as an expense, not an investment, and those who oversee these storerooms have difficulty securing the funding necessary to properly staff their department and make improvements that would better the department’s efficiency and benefit the entire organization.
Those in charge of approving the facility’s budget are okay with cycle-counting out thousands of dollars worth of spare parts, misguidedly believing it’s just part of doing business. As long as the assets are repaired and put back into production, they are content to sweep larger underlying problems under the rug. This mentality can have costly repercussions for the entire organization.
But, by recognizing the impact an MRO storeroom can have and taking steps to ensure its efficiency and advancement, an organization can reduce its costs, increase its uptime, and guarantee the success of its associates.
Keys to MRO Storeroom Success
The MRO storeroom associate is key to ensuring parts are readily available for an organization’s maintenance program. It’s common for these organizations to have MRO associates work closely with the receiving department to ensure the items being received match what was ordered and are not damaged.
While this is a good practice, unfortunately, I have found during my facility visits that many times, these associates are not trained properly in this process. Oftentimes, the only training they receive is how to:
- Use the current system to look up and issue parts.
- Put stock away.
- Process a return.
- Complete any necessary 5S activities.
5S
A Japanese-based set of principles designed to eliminate waste and foster a workplace culture of efficiency.Source: Reliable Plant
However, to be successful, associates must also know:
- What the part is supposed to look like.
- How to review the parts for damage.
- How to store parts properly.
- What special storage needs each part has.
- How to perform preventive maintenance (PM).
- How to conduct cycle counts.
When asked why these organizations don’t provide this crucial training, I’m met with the typical answer, “We don’t have the time.” This leaves the responsibility of completing these tasks to the purchasing/receiving department, which is often short on time.
Developing a Training Program
It’s important for organizations to develop a world-class training program for all MRO storeroom associates to guarantee the health of all maintenance parts and materials used to support the maintenance of critical facility assets.
These training programs also develop a sense of pride and responsibility in the MRO associates, who become better equipped to understand and assist the maintenance technicians with any of their needs and requests. MRO and plant maintenance must partner together to ensure the facility experiences minimal downtime and produces a quality product for its customers.
Understanding the Inventory System
Training needs to begin with understanding how the organization’s specific inventory system operates. During this time, associates should spend time at the receiving dock to gain knowledge of how the receiving process works and how purchase orders are updated in the system after they have been received.
Performing Inspections
Next, associates should learn the inspection process. This includes:
- Visually inspecting for any damage to the parts.
- Reviewing labels and tags for specific part numbers.
- Verifying the parts were properly shipped and stored.
It is also a good idea for the receiving associates to train the MRO associates on how to locate, review, and understand the different parts of the purchase order, such as:
- Item numbers.
- Quantities.
- Order dates.
- Expected delivery dates.
- Vendor information
This information is extremely useful for answering any questions the maintenance team may have about a particular part.
Operating Heavy Equipment
Finally, all MRO associates must be trained on how to operate heavy equipment, such as:
- Lift trucks.
- Tuggers.
- Carts.
- Other electric transportation vehicles.
Many times, I have found that if an organization does provide this training, it’s only for one or two MRO associates. This tactic ends up causing delays in getting the necessary parts to the maintenance team, which hinders their ability to fix downed equipment in a timely manner.
Organizing an MRO Storeroom
Once received, the MRO associates must understand how to appropriately put each part away in the storeroom, carefully considering any unique requirements they may have. For example, ball screws should be stored either completely vertically or horizontally on V-blocks and at a specific temperature to prevent bending.
If questions arise concerning how to properly store a specific item, many vendors and suppliers are more than happy to visit the storeroom and help train the associates.
The ABCs of MRO Storerooms
The MRO associate should understand how to conduct cycle counts of parts and be aware of what the top movers are in the storeroom. Most organizations use the ABC method to determine what items need to be counted.
“A” items typically make up 80% of the total inventory value, but only 20% of the SKUs carried.
“B” items typically make up 15% of the total inventory value, but only 30% of the SKUs carried.
"C" items typically make up 5% of the total inventory value and are 50% of the SKUs carried.
ABC Method
"An inventory management technique that determines the value of inventory items based on their importance to the business. ABC ranks items on demand, cost, and risk data, and inventory managers group items into classes based on those criteria."Source: NetSuite
This classification method is a good starting point. Many organizations will regularly count the top 25 to 50 SKUs moving through their system. This ensures the parts in the highest demand are always kept in stock and that reviews of the minimum and maximum number of products on hand are conducted at regular intervals. This information is then provided to a manager who reviews the results and makes any necessary changes to keep the parts on hand at an optimal level.
Spare Parts Preventive Maintenance
MRO associates must also understand how to perform preventive maintenance on the spare parts. This includes:
- Turning the shafts on motors per manufacturer guidelines to redistribute grease and prevent false brinelling.
- Ensuring that belts are properly stored to prevent premature failure and that they are issuing the oldest belts first and rotating newer stock to the back.
- Working bearings to prevent brinelling.
- Checking that hydraulic cylinders are stored vertically to prevent actuator seal damage.
While organizations can outsource PM duties to a third party, it is still important for storeroom associates to understand these requirements so they can do their part to ensure these items are stored correctly as soon as they are received and put into inventory.
Assigning Responsibility
All MRO storeroom associates should be assigned an area where they are responsible for conducting 5S activities and providing upkeep for the items in that area. This could include:
- Conducting cycle counts.
- Inspecting for damage and improper storage.
- Performing preventive maintenance.
- Ensuring all parts are correctly labeled and in the right location.
This practice also fosters a sense of pride by having associates become “experts” in their area. As a bonus, many times, the associates can help identify needed corrections in another associate’s area that may have been missed by providing a fresh pair of eyes.
Assigned areas can be rotated on a quarterly basis to help the associates become familiar with all areas of the storeroom.
MRO Storeroom Classes
Finally, it is important to provide the opportunity for associates to attend formal MRO storeroom classes. These classes cover:
- Ways to set up and maintain a storeroom.
- How to stock parts in the right quantities.
- Preventive maintenance programs.
- Purchasing procedures.
- The roles and responsibilities required to properly maintain a storeroom.
Whether they are a new employee or a manager, all storeroom associates can benefit from attending MRO classes, which provide excellent knowledge that leads to tangible results for the entire organization, such as increased wrench time, reduced defects, and decreased spending.
Conclusion
It’s crucial for MRO storeroom associates to have a training plan just like other departments across the facility to be set up for success. The storeroom is one of the most important departments in the entire facility, but until it is given the necessary training and financial investment, the benefits it can provide won’t be experienced. A great MRO associate is an invaluable asset to any facility.
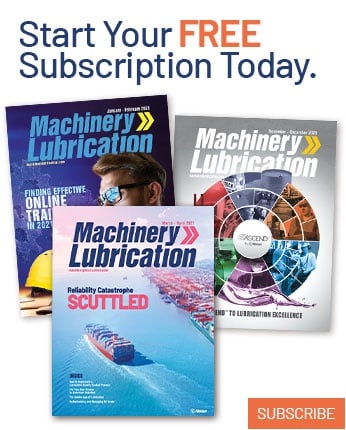