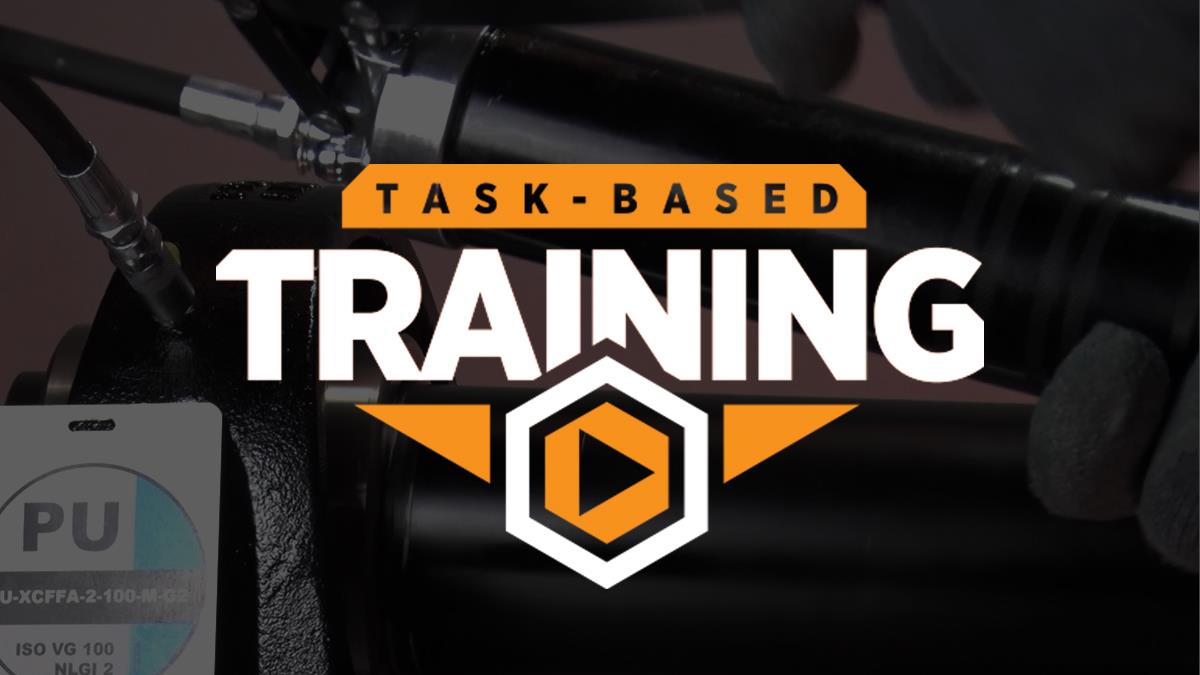
Why Regrease a Bearing?
While used in components such as bearings, grease tends to degrade over time. As the oil separates from the thickener, it can lead to oxidation, and lubricant starvation can occur inside that bearing. The oil pathways within the bearing can also become contaminated and lead to abrasion, fatigue, and failure.
So, regreasing the bearing allows for refreshing the lubricant, maintaining the lubricating films, and displacing some of the old grease that may be contaminated, thus providing a better lubrication regime for that bearing. This, in turn, extends the life of the bearing and minimizes downtime.
Why Do We Use Grease?
Grease is a common lubricant in industrial machinery due to its unique properties that make it well-suited for various applications and environments. Different types of greases are formulated with specific properties to suit various bearing applications, considering operating speed, temperature, load, and environmental conditions. Regular greasing and maintenance are essential to ensure that bearings operate smoothly and efficiently over their intended lifespan.
Cautions When Using Grease
One of the things to remember when regreasing a bearing that hasn't been touched in a while is that the thickener can harden within the bearing as the base oil separates over time, and all that's left is the dried, caked-on thickener. As you add pressure on the bearing, all those hard chunks will be sent into the load zone. This is akin to adding gravel to the bearing, which can cause significant wear and tear and eat away at the metal.
An excellent way to lessen this damage or prevent any injury from the application would be to open the purge port, if available so that the hard matter and contaminants can be pushed out of the bearing cavity. Remember, it is essential to check that the purge point pathway is clear.
What Does Improper Greasing Cause?
Overgreasing is typically the most common mistake in a plant. This causes excess friction and heat, which can lead to the degradation of the lubricant and the bearing itself. Over-greasing also causes the grease to purge through the seals, allowing a pathway for contaminants to enter and cause considerable damage.
On the other hand, under-greasing can lead to metal-on-metal contact, excessive friction, and the dreaded squealing sound that all but indicates that bearing is on its way out soon.
What Are Some Different Types of Grease Guns?
-
Lever – easy-to-use, manual lever for application; most popular
-
Pistol grip – common-use grease gun, used in ultrasonic applications
-
Pneumatic – powerful grease gun that uses compressed air
-
Electric – battery-operated, typically used in large-scale industrial applications
The lever grease gun is handy, allowing you to feel the pressure as you add grease. So, if you have a blockage, you'll know to stop, take apart, and purge that line before regreasing.
It is also essential to use the right gun for the right grease. Although the different types of grease guns can look alike, each gun is used for a different type of grease application, and it's crucial to have each grease gun labeled that also matches the label on the grease.
Over time,
grease guns can also get out of calibration, so the right grease for the right application will ensure the gun's accuracy and effectiveness over a more extended period.
How Much Grease to Use?
Many factors determine the right amount of grease for any application. We've covered that adding too much or too little grease can significantly (and negatively) affect your application, so typically, it must be determined by proper calculation.
Two key factors that help determine how much grease to use are the speed at which the bearing will spin as well as the size of the bearing. Along with the inner and outer diameter, you'll need to determine how big the cavity is and how much grease it will take to fill it.
In other words, the physical dimensions of the bearing do much of the dictating on determining grease volume.
Picking the Right Grease Gun
Once you've done the math on the bearing size and spin speed, it is also important to
determine the correct grease gun to use. Having a postal scale can be very useful in this step.
Being able to pre-weigh each shot from each grease gun will help you figure out how much the grease gun is dispersing.
A simple rule is understanding how much output results from a half-shot of grease. This understanding is crucial before entering the field and using the grease gun.
How Often Do We Need to Regrease a Bearing?
The frequency of regreasing a bearing depends on various factors, including the type of bearing, the application, operating conditions, load, speed, and grease used. Generally, there is no one-size-fits-all answer, but here are some general guidelines to consider:
Manufacturer Recommendations: The bearing manufacturer often provides guidelines for lubrication intervals. These recommendations are based on their understanding of the bearing's design, materials, and intended use. It's essential to follow these guidelines as a starting point.
Operating Conditions: Harsh operating conditions, such as high temperatures, heavy loads, high speeds, and contaminant exposure, can accelerate grease breakdown. In such cases, more frequent regreasing may be necessary.
Lubrication Type: Different greases have varying properties, including their ability to withstand heat, load, and speed. Some greases are designed for long-lasting performance, while others may require more frequent regreasing. Consult the grease manufacturer's specifications for guidance.
Condition Monitoring: Regular monitoring of bearing performance can help determine the need for regreasing. Monitoring can include measuring temperature, vibration, noise levels, and overall bearing condition. An increase in temperature or abnormal vibrations could indicate inadequate lubrication.
Experience and History: Over time, operators and maintenance personnel may understand how often regreasing is required based on historical data and observations.
Automated Lubrication Systems: Some industrial machinery uses automated lubrication systems that can be programmed to deliver precise amounts of grease at specific intervals. These systems can help ensure consistent and proper lubrication.
Application Type: Different applications have different demands. Bearings used in heavy industrial machinery might require more frequent regreasing than those used in lighter-duty applications.
Preventive Maintenance Schedule: Incorporating bearing regreasing into a routine preventive maintenance schedule helps ensure that lubrication is not neglected.
Remember that
over-greasing can be just as harmful as under-greasing. Excessive grease can lead to increased heat, friction, and a buildup of contaminants, causing more harm than good. Proper training and using the right amount of grease are essential.
It's essential to consider the factors mentioned above and work closely with equipment manufacturers and maintenance experts to determine the most suitable regreasing schedule for your specific machinery and operating conditions. Regular inspection, monitoring, and adjustment of the regreasing frequency based on performance and conditions will help ensure optimal bearing performance and extend lifespan.
Who Should Do Greasing?
Lube techs, operators, and maintenance personnel — in other words, trained professionals — should be the central figures who determine grease and regrease needs. You can think of a grease gun as a loaded weapon. When working within a lube team and different reliability programs, you want to ensure the person operating that grease gun understands that and follows the proper guidelines and safeguards discussed in this lesson.
How to Regrease a Roller Bearing with a Grease Gun
-
Gather all the appropriate tools required to perform the procedure.
-
Verify that the grease gun's LIS code matches the recommended lubricant used in the roller bearing.
-
Clean the roller bearing’s external surface and area around it using a brush and a lint-free industrial towel.
-
Remove the plug if fitted from each purge port and clean any hardened grease with a pipe cleaner or wire.
-
Remove the dust cap if fitted from each grease fitting and clean up any grease with a lint-free industrial towel.
-
Attach the grease gun nozzle to the grease fitting. (Do not hold the nozzle with your hand while applying grease.)
-
Place a waste grease container beneath the purge port.
-
Slowly apply up to the maximum of regrease volume of recommended lubricant.
-
If grease is observed purging from the component, discontinue greasing and make note of the volume added. (Do not exceed the calculated maximum regrease volume for the component.)
-
Stop pumping and disconnect the grease gun.
-
If you feel abnormal back pressure while pumping grease, stop greasing and check for an obstruction in the grease passages.
-
Use a pipe cleaner or a wire to clean and remove hardened grease from the grease and purge ports.
-
Clean the grease fitting and replace the cap.
-
Wipe the grease gun nozzle and replace the cap.
-
Wipe up all grease purged from the relief port.
-
Replace the plug if fitted on the purge port.
-
Collect and properly dispose of the waste grease and consumables used during the procedure.
Key Takeaways
-
Choose the proper grease.
-
Lubricate the equipment while the machine runs (if possible) to get the proper grease displacement throughout the cavity.
-
Make sure the coupler and fitting are clean before starting the lubrication process.
-
Open purge port if applicable.
-
Always practice good safety and wear your PPE.
About the Author