Building a world-class lubrication program is a multistep process. A widely advocated, classic approach is to begin by benchmarking the current performance, followed by defining opportunities and designing and documenting the practices required to exploit the opportunities, and finally implementing the designed program.
Each of these steps has its challenges and as most of us are aware, implementation is often the most difficult step. After all, it’s human nature to resist changing the way we do things.
When teaching lubrication seminars, I spend a lot of time teaching easy ways to improve lubrication. When discussing these points, one of the most common objections I hear is "I know we should be doing this, but how do I get my people to actually do it?"
One answer to this question is to rigorously define and document every routine and nonroutine activity, then make that information available in an accessible and usable format. However, this in no way guarantees success; rather it is only one part of the solution.
While this practice is a must for long-term success, it is equally important to educate individuals on the performance of these tasks and more importantly the underlying reasons for performing the tasks in accordance with the defined best practice. In many cases, simply telling people to do something a certain way will not ensure that it happens.
When it comes to executing the details of a well-designed lubrication program, the importance of "why" is often equal to or greater than the importance of "what". I myself am disinclined to do something if I don't understand its value. This may sound like a pessimistic view, but it is not.
I don't believe that people just choose to ignore the instructions they have been given or worse yet, that they prefer to do a substandard job. I believe that they have been acclimated or encouraged to do things their own way to improvise or find efficiencies in the performance of the jobs to which they are assigned.
While this is often a good way of uncovering new opportunities, changes to defined operating procedures must be controlled by a well-thought out management of change (MOC) procedure.
With the proper academic knowledge of lubrication fundamentals, the individuals involved in the lubrication program will most often embrace best-practice procedures and offer valid recommendations for changes rather than simply substituting their own opinions for how a task should be performed.
A common example of an excellent practice often compromised by insufficient training is the use of lubricant identification tags to prevent cross-contamination of lubricants. If you're reading this article, you are likely aware of the implications of mixing incompatible lubricants or using the wrong lubricant.
You also understand that using a lubricant ID tagging system will go a long way toward eliminating this common problem. If you simply tag each lubricated component, transfer device and storage container with an identification code, this should effectively eliminate cross-contamination … right? Not necessarily. You must consider every individual who might add oil or grease to a particular machine.
If he or she does not understand the reason for using the specified lubricant or the implications of using the wrong lubricant, he may mistakenly top-up a machine with the most accessible product or his favorite product that works well in another application.
I was once told a story of two electrical engineers who took some turbine oil home to use in their cars. They concluded that because the turbine oil was an extremely high-quality lubricant - one used in a critical and costly application - that it must be better than the common engine oil they were currently using.
Of course the turbine oil was neither the right viscosity, nor did it contain the necessary additives to effectively lubricate the engines. As a result, both cars failed in short period of time.
The point is, that both of these people were aware of what oil they were supposed to use according to the OEM, but because they didn't understand why, they made an uninformed choice and paid the price.
While the story of the two engineers usually brings a few laughs when I tell it, consider the economic impact when a similar event occurs in your plant and how preventable this common mistake is.
When decisions are made to make improvements to your program, it is crucial that you decide what knowledge and to whom it must be disseminated to facilitate and ensure the quality of implementation and execution of these items. It is important that education and training become a core component of your lubrication program.
I recommend establishing appropriate levels of training and competence for everyone who affects lubrication. Not everyone needs to be a certified expert, but everyone should have a certain level of expertise according to his or her role. Education will not only ensure adherence to your defined best practices but it will also ensure continuous improvement for years to come.
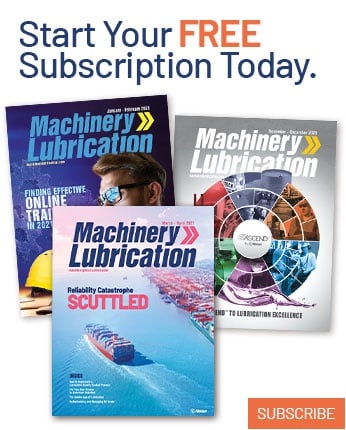